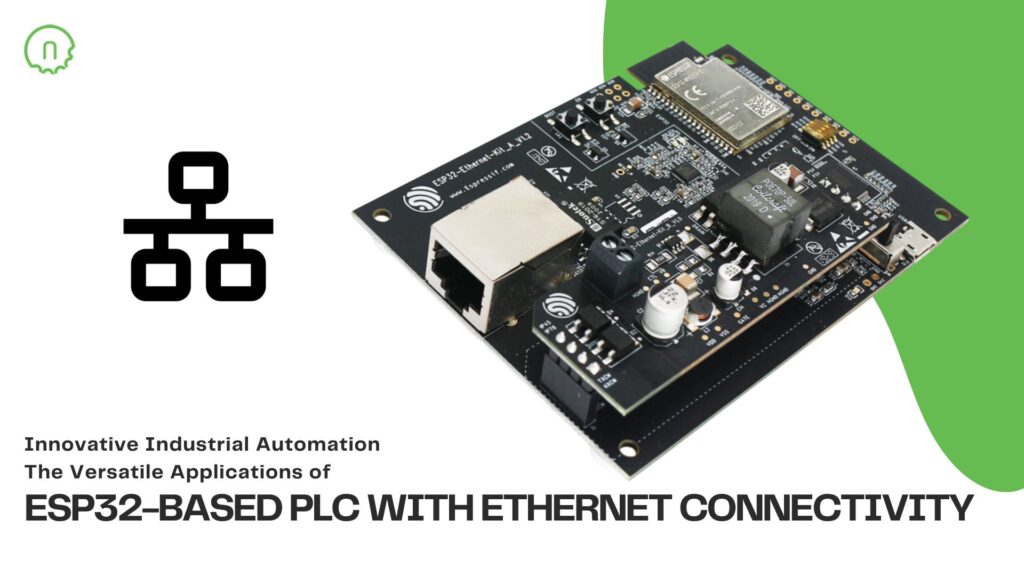
Why ESP32-based PLC with Ethernet Connectivity? In today’s dynamic industrial landscape, the demand for efficient and reliable automation solutions continues to grow. The advent of technologies like the ESP32-based PLC with Ethernet Connectivity has revolutionized the realm of industrial automation. These powerful devices offer a wide array of applications, transforming the way industries operate and optimize their processes.
What is Ethernet?
Ethernet is a widely used technology that defines a system for connecting a group of computers and other devices in a local area network (LAN). It was developed in the 1970s by Xerox Corporation’s Palo Alto Research Center (PARC) and later standardized by the Institute of Electrical and Electronics Engineers (IEEE).
Ethernet operates on the principles of packet-switching and uses a set of protocols to enable devices within the same network to communicate with each other. It involves physical cabling (such as twisted pair, fiber optic, or coaxial cable) and a series of rules and procedures for transmitting data between connected devices.
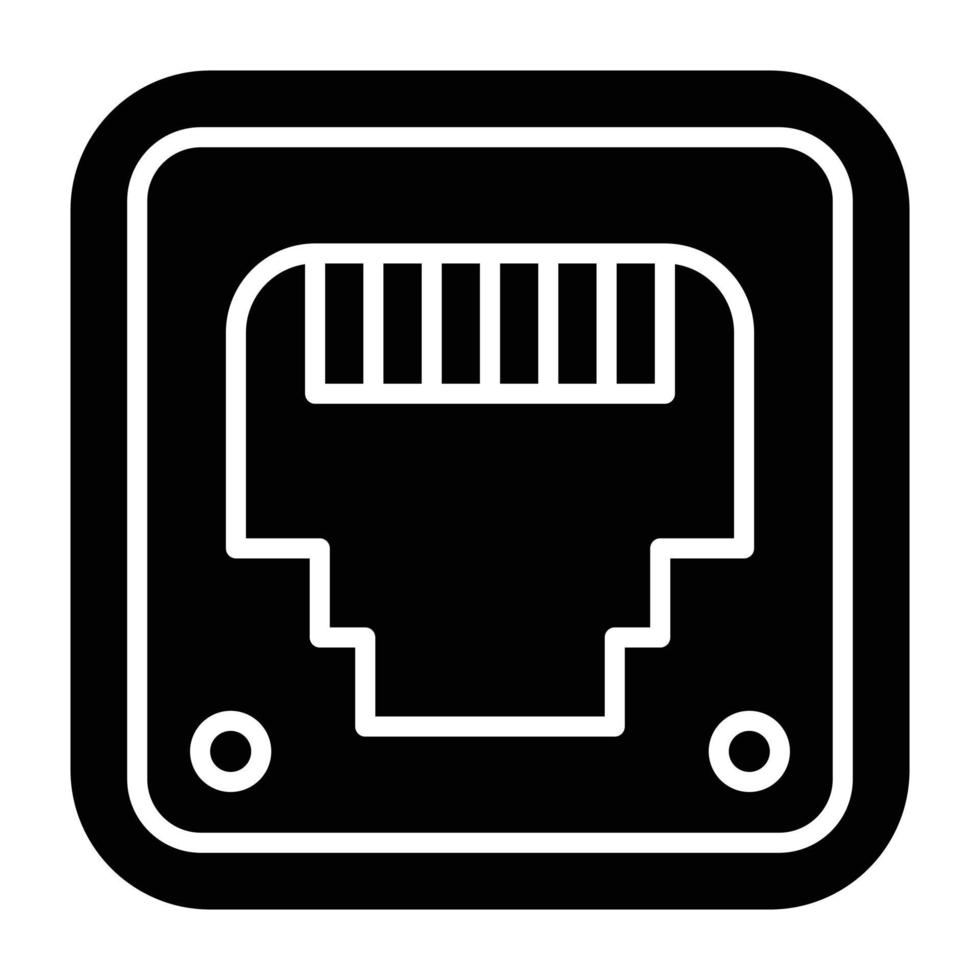
Some key aspects of Ethernet include:
- Data Transmission: Ethernet networks use frames to transmit data between devices. These frames contain information about the sender, receiver, type of data, and error-checking bits.
- Speeds: Ethernet has evolved over the years to support various speeds, ranging from the original 10 megabits per second (Mbps) to 100 Mbps, 1 gigabit per second (Gbps), 10 Gbps, 40 Gbps, 100 Gbps, and even higher.
- Topologies: Ethernet supports various network topologies, including star, bus, and ring configurations. The most common nowadays is the star topology, where devices connect to a central switch or router.
- Standardization: IEEE 802.3 defines the standards for Ethernet, ensuring compatibility and interoperability between devices from different manufacturers.
- Usage: Ethernet is widely used in homes, businesses, data centers, and various industries as the primary means of local area networking.
Ethernet has undergone numerous advancements and improvements, allowing for faster speeds, increased reliability, and greater flexibility in network setups. It remains one of the most prevalent and fundamental technologies for networking, enabling communication between devices within a local network environment.
ESP32-based PLC with Ethernet
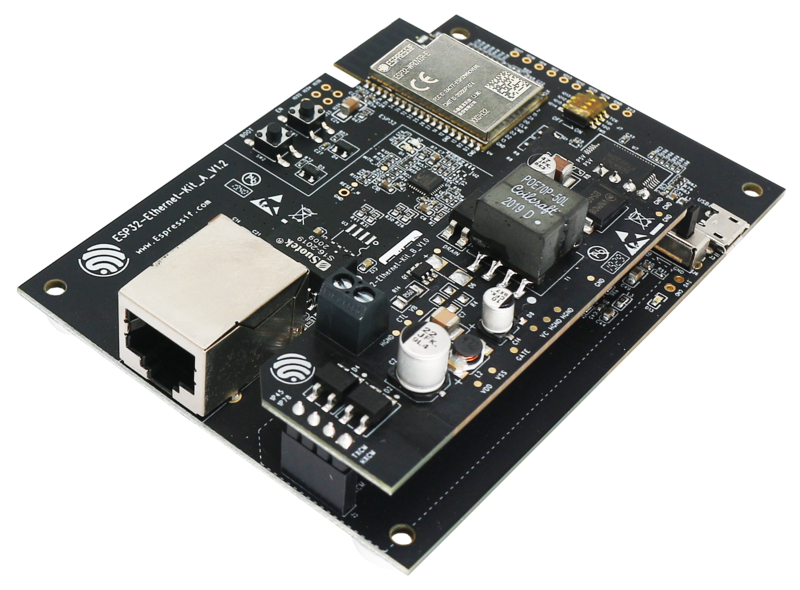
An ESP32-based PLC with Ethernet Connectivity can offer several advantages and capabilities due to the combination of the ESP32 microcontroller and Ethernet connectivity:
- Networking Capabilities: Ethernet connectivity enables the PLC to communicate with other devices, such as computers, servers, sensors, and other PLCs, over a local area network (LAN). This allows for data exchange, control, and monitoring of industrial processes or automation systems.
- Reliability and Speed: Ethernet provides a stable and reliable communication platform with high-speed data transfer rates. This is crucial in industrial settings where real-time data processing and communication are required for efficient operations.
- Integration with Existing Infrastructure: Many industrial environments already have established Ethernet-based networking infrastructure. Using an ESP32-based PLC with Ethernet allows seamless integration into these systems without requiring significant modifications or additional hardware.
- Remote Monitoring and Control: With Ethernet connectivity, the ESP32-based PLC can enable remote monitoring and control functionalities. This means that operators or engineers can access and manage the system from a central location, improving efficiency and reducing the need for physical presence on the factory floor.
- Scalability and Flexibility: Ethernet-equipped PLCs can easily scale to accommodate larger systems or expand functionalities by leveraging network capabilities. They can also interact with a variety of devices and systems, providing flexibility in industrial automation setups.
- Security Features: Ethernet-based communication can leverage various security protocols and measures to ensure data integrity and prevent unauthorized access, enhancing the overall security of industrial networks.
- Compatibility and Standardization: Ethernet is a well-established and standardized networking technology, ensuring compatibility with a wide range of devices and systems, and facilitating easier integration and interoperability.
Why Ethernet stands out?
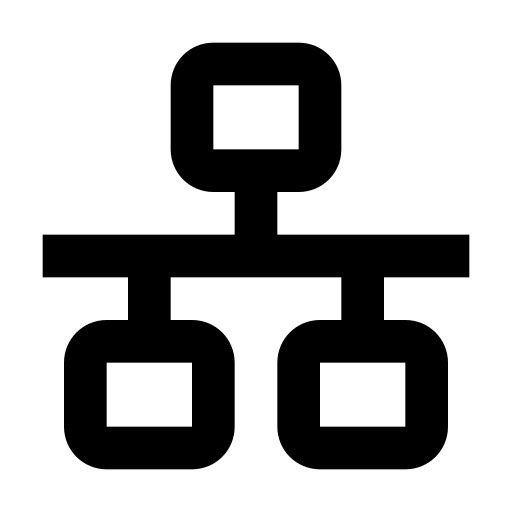
While other connectivity options like serial communication (RS-232, RS-485), Fieldbus protocols (Profibus, Modbus), wireless technologies (Wi-Fi, Bluetooth, Zigbee), or proprietary industrial protocols have their own merits, Ethernet stands out due to its speed, reliability, scalability, and standardization, making it an excellent choice for connecting PLCs in modern industrial automation setups. Additionally, advancements in Ethernet technology continue to enhance its capabilities, making it more adaptable and suitable for diverse industrial applications.
ESP32-based PLC with Ethernet Connectivity enhances its capabilities, enabling robust communication, remote access, scalability, and integration into existing industrial networks, thereby improving the efficiency and effectiveness of industrial automation and control systems.
Applications in Industrial Automation
There are various applications that can perform using ESP32-based PLC with Ethernet Connectivity effectively. Find below:
1. Factory Automation and Control
ESP32-based PLCs with Ethernet play a pivotal role in controlling and supervising industrial machinery and processes. They enable precise and real-time control of production lines, ensuring seamless operation, minimizing downtime, and optimizing overall efficiency. These PLCs manage diverse tasks, including motor control, conveyor systems, and robotic operations.
2. Remote Monitoring and Management
Ethernet-equipped PLCs empower remote monitoring and management of industrial setups. Engineers and operators can access critical data, monitor machine performance, and troubleshoot issues from a centralized location. This capability streamlines maintenance procedures, enhances operational visibility, and facilitates timely interventions, reducing maintenance costs and increasing uptime.
3. Integration into Existing Networks
The compatibility of ESP32-based PLCs with Ethernet facilitates easy integration into existing industrial networks. They seamlessly communicate with other devices, such as sensors, Human Machine Interfaces (HMIs), and servers, leveraging standardized Ethernet protocols. This integration optimizes workflow, data exchange, and interoperability among various components of the automation ecosystem.
4. Data Acquisition and Analysis
These PLCs efficiently collect and process data from sensors and connected devices. With Ethernet connectivity, they transmit this data to central servers or cloud-based platforms for in-depth analysis. By harnessing this data, industries gain valuable insights into production trends, anomalies, and predictive maintenance, empowering informed decision-making.
5. Enhanced Security Measures
Ethernet-based communication in ESP32-based PLCs incorporates robust security measures, safeguarding sensitive industrial data and preventing unauthorized access. Encrypted communication protocols and authentication mechanisms ensure the integrity and confidentiality of data exchanged within the network.
NORVI ESP32-based PLC with Ethernet
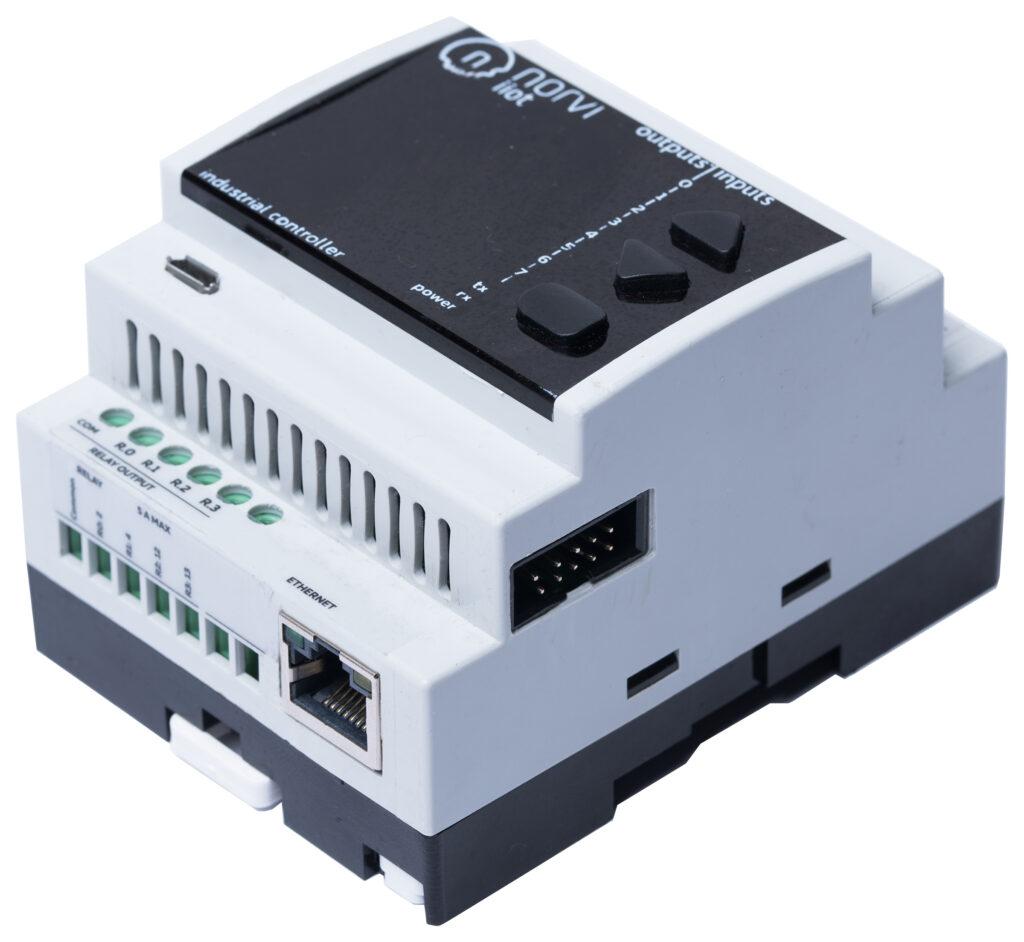
The marriage of ESP32-based PLC with Ethernet Connectivity heralds a new era in industrial automation. These versatile devices offer a spectrum of applications, revolutionizing manufacturing, process control, and operational efficiency. By enabling seamless connectivity, precise control, remote management, and enhanced data analysis, these PLCs are pivotal in shaping the future of industrial automation.
As industries continue to evolve, embracing the capabilities of ESP32-based PLC with Ethernet Connectivity will undoubtedly remain a cornerstone in achieving higher productivity, reduced downtime, and smarter decision-making in the industrial landscape.
Visit our product page now to buy ESP32-based PLC with Ethernet: https://norvi.lk/product/industrial-esp32-ethernet/
#NORVI #ESP32 #ESP32PLC #Ethernet #EthernetAutomation #IndustrialESP32 #PLCTechnology #AutomationSolutions #SmartManufacturing #IoTIndustrial #ConnectedPLC #DigitalFactory #Industry40 #EthernetPLC #AdvancedAutomation #ESP32Innovation #EfficientPLC #ReliableAutomation