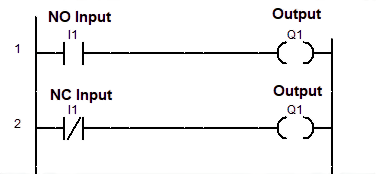
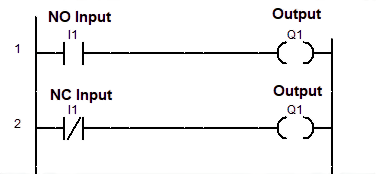
What is a PLC?
A Programmable logic controller (PLC) is a special purpose computing device designed for use in industrial control systems and other systems where the reliability of the system is high. The goal of a PLC was to replace electromechanical relays as logic elements with a solid-state digital computer with a stored program that could simulate the connectivity of numerous relays to execute specific logical tasks. But today they have scaled and are being used by all kinds of manufacturing processes including robot based lines.
What is Ladder Logic?
Ladder logic is one of the most widely used PLC programming languages in industry. It is a graphical programming language for PLCs that uses symbols that are similar to those used in wiring diagrams. It’s simple to understand and use, and has been adopted since the early days of Programmable Logic Controllers.
Replacing PLCs in Industrial Applications with Microcontrollers
Microcontrollers are tiny computer devices containing one or more processor cores, memory devices, and programmable special and general purpose input and output (I/O) ports on a single chip. They are employed in a variety of everyday devices, particularly in situations where just specified repeated actions must be completed.
The introduction of microcontroller-based boards in recent years has increased interest in embedded systems, allowing a large number of people to enter the realm of microcontrollers. This has expanded not just the number of people who utilize microcontrollers, but also the range of applications for which they are employed. They’re currently being used in a variety of applications where microcontrollers were previously thought to be ineffective, ranging from small DIY computers to sophisticated control systems. This has raised questions as to why microcontrollers aren’t utilized instead of PLCs. The main arguments kept are,
- PLCs are built to survive harsh conditions, while microcontrollers aren’t. As a result, they are unsuitable for commercial use.
- Industrial sensors and actuators are often constructed to the IEC standard, which specifies a range of current/voltage and interfaces that may or may not be directly compatible with microcontrollers, necessitating the purchase of additional hardware.
NORVI Controllers Solution
Norvi Industrial controllers are programmable IoT devices based on micro-controllers. Unlike the usual controllers, these devices are designed with ruggedness and the ability to withstand extreme conditions, which makes them ready for industrial applications.Also they are designed according to the IEC standard which is usually at a range of current/voltage and interfaces for industrial applications.
Programming these devices is made easier by allowing users to code them using simple platforms such as the Arduino IDE, which includes step-by-step instructions. Depending on the model, these ESP32-based devices are equipped with digital and analog I/O, allowing them to detect digital logic states and analog inputs. Variety of models in the Norvi lineup are capable of measuring the environmental factors like flow rate, pressure, temperature and offer analog inputs (for dedicated voltage/current measurement) at the industrial level.
If Norvi Controllers are micro-controller based products then how Ladder programming becomes possible with them?
The open source project by Leonardo Fernandes that generates Arduino code for ESP32 based micro-controller devices has given a solution for this. It’s a desktop based Java application developed with Eclipse IDE + WindowBuilder plug-in.
We have written a step by step application note on how to program ladder logic for Norvi controllers. –https://www.instructables.com/Ladder-Logic-Programming-for-ESP32-Based-Controlle/
Also check this link to know more about the open source project by Leonardo Fernandes. –https://github.com/leofds/iot-ladder-editor